WHY CONSIDER SPHERONIZATION?
The products produced from this process can be useful in several ways:
- Product performance and functionality can be improved or changed to meet a wide range of requirements
- Plant procedures can be simplified, to reduce costs or enhance security of operation
The process is well known and widely used in the pharmaceutical, neutraceutical, catalyst, petrochemical, materials science and other industries. Its use is becoming increasingly recognized in other areas of industrial material handling.
WHAT IS THE BASIC EQUIPMENT FOR THE PROCESS OF SPHERONIZATION?
The process of spheronization consists of four key steps:-
- Mixing or granulation (a mixer or granulator is required)
- Extrusion (an extruder is required)
- Spheronization (a spheronizer is required)
- Drying and possibly coating (a coater and drier may be required)
All of these steps are important and all can have a considerable influence on the final product performance.
Mixing and/or Granulation:
The influence of different mixing/granulating parameters should not be underestimated. It is true that in many cases mixing can have little or no effect on the process or final product performance but this should never be assumed. When doing development work, it is important to keep the mixing/granulation parameters constant (to remove a potential source of variation) or to make systematic trials and demonstrate the effect (or lack of effect) of changes in the mixing parameters.
Extrusion
The extrusion of the materials is a required step prior to spheronization. The final size of the pellets is principally determined by the diameter of the extrudate used for the spheronization process. For example in order to obtain spheres with a diameter of about 1 mm, a 1 mm diameter hole is used on the extruder die or screen, although dies and screens with slighter larger hole diameters will sometimes be used to allow for shrinkage on drying. In a spheronizer, it is possible to obtain spheres with a diameter ranging from about 0.4 mm to about 8 mm.
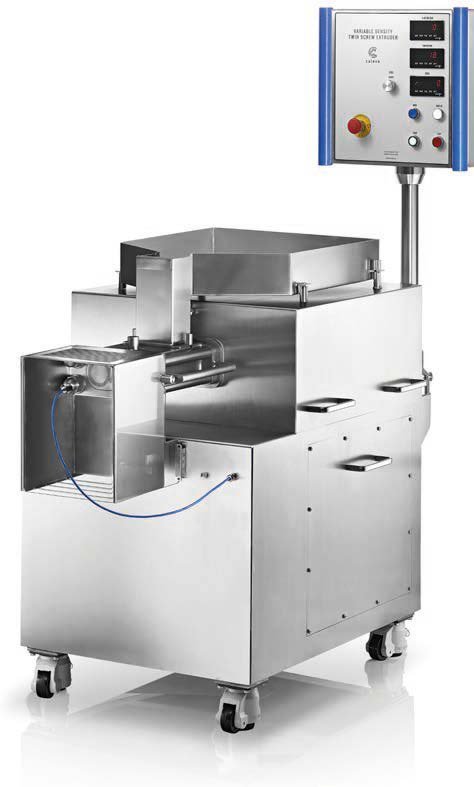
Spheronization
Modern spheronizers have several additions and adaptations depending upon the needs of the particular product and process. The design principle of the spheronizer is relatively simple but the detailed development of auxiliary equipment and the specifics of the design have widened the range of applications and greatly improved the flexibility of the machines

In principle the basic machine consists of a round disc with rotating drive shaft, spinning at high speed at the bottom of a stationary cylindrical bowl. The spinning friction plate has a carefully designed groove pattern to the base. This is most often cross-hatched, but several sizes and other types are available. These discs are designed to increase the friction with the product.
Extrudates are added to the spheronizer and they fall onto the spinning plate. During the early contacts of the cylindrical granules with the friction plate, the extrudates are cut into segments with a length ranging from 1 to 1.2 times their diameter. These segments then collide with the bowl wall and they are thrown back to the inside of the friction plate. Centrifugal force sends the material to the outside of the disc.
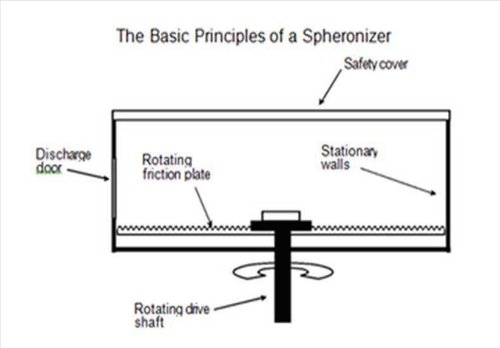
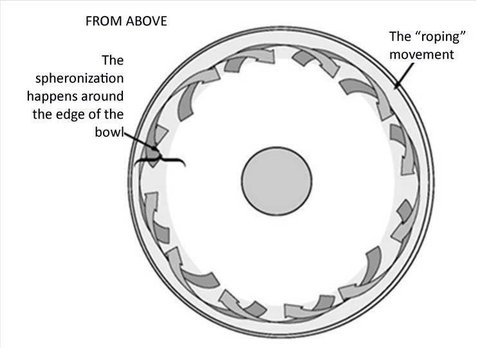
The action of the material being moved causes the extrudate to be broken down into pieces of approximately equal length relative to the diameter of the extrudate. These cylindrical segments are gradually rounded by the collisions with the bowl wall, the plate and each other. The ongoing action of particles colliding with the wall and being thrown back to the inside of the plate creates a “rope movement” of product along the bowl wall. The continuous collision of the particles with the wall and with the friction plate will gradually turn the cylindrical segments into spheres, provided that the granules are pliable enough to allow the deformation without being destroyed. It is essential that this rope movement is present for an optimal spheronization.
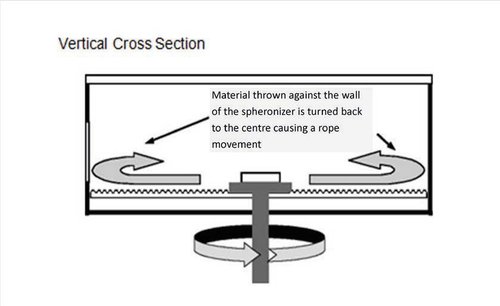
As processing continues, the shape of the pieces gradually changes as shown below.
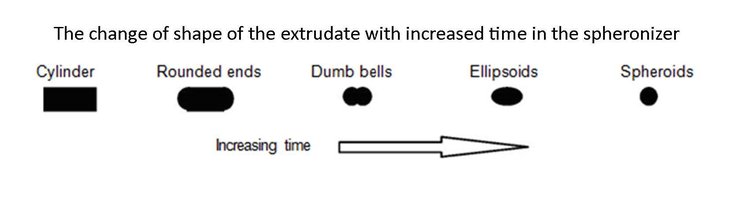
When the particles have reached the desired shape (usually in about 2 to 10 minutes) then the spheroids can be removed.
The photographs below show the process of change in the spheronizer. When the particles have obtained the desired spherical shape, the discharge valve of the spheronization chamber is opened and the granules are discharged by the centrifugal force.
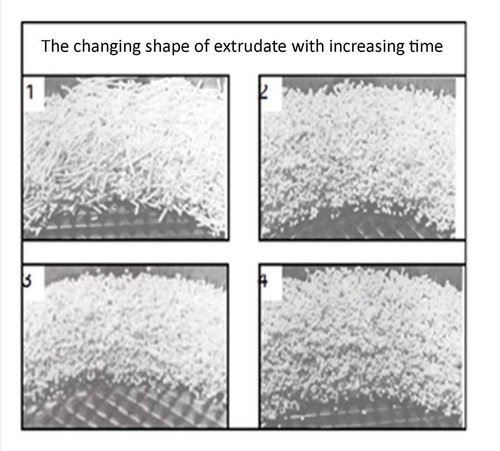
WHAT ARE THE KEY PROCESS PARAMETERS?
The process parameters can be split into those related to the spheronizer equipment itself and those related to the product used. All these parameters have to be in harmony to obtain a good process result.
Machine Parameters
Friction plate pattern
The most common groove pattern used for spheronizer discs is the “waffle-iron” design, where the friction plate is like a chessboard of chopped-off pyramids. The choice of which plate to use is not always clear. As a guideline extrudates up to 0.8 mm in diameter are normally processed on a 2 mm pitch plate. A 3 mm pitch plate is used for extrudates up to 3 mm in diameter. Discs with a radial design are also used, as these are considered gentler on the material being spheronized.
Friction plate pattern
The most common groove pattern used for spheronizer discs is the “waffle-iron” design, where the friction plate is like a chessboard of chopped-off pyramids. The choice of which plate to use is not always clear. As a guideline extrudates up to 0.8 mm in diameter are normally processed on a 2 mm pitch plate. A 3 mm pitch plate is used for extrudates up to 3 mm in diameter. Discs with a radial design are also used, as these are considered gentler on the material being spheronized.
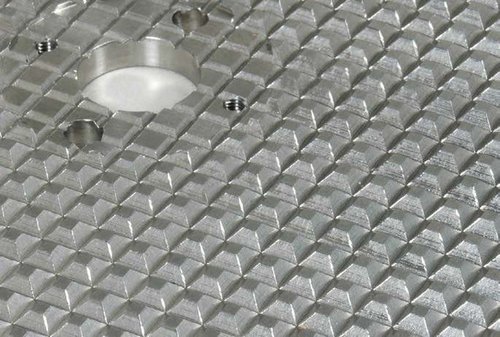
Friction plate speed
The typical rotation speed of a production size (700 mm diameter) disc ranges from 200 to 450 rpm. The higher the speed, the more energy is put into the particle during a collision. The optimum speed depends on the characteristics of the product being used and the particle size. The smaller the diameter of the disc the higher the speed required. The important parameter is the speed at the outer edge of the disc. In practice the optimum speed can be determined with a little experience. For some products it may be recommended to start at a high speed and to lower the speed in the final stage of the process. This can be determined by simple practical tests. The process allows a high degree of flexibility for good formulations.
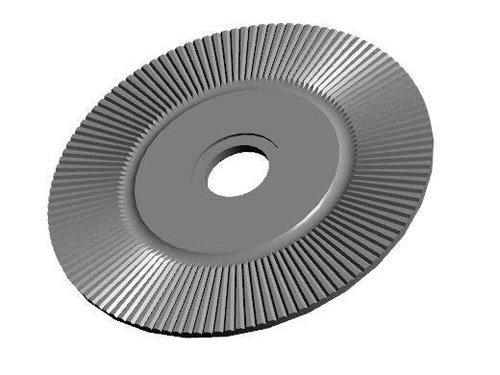
Retention time (The length of time the product is spheronized in the spheronizer)
Typical spheronization retention times to obtain spheres range from 3 to 8 minutes. This is relatively easy to determine and best obtained by simple trials with specific products. For some products, the strong cohesive forces in the extrudates prevent the extrudates from breaking up into smaller pieces. If the objective is to reduce dust and not necessarily obtain perfect spheres then the short contact with the friction plate is sufficient to break the long extrudates into small segments and round the edges. The edges of cylindrical granules are the most fragile part and they will generate dust during handling and transportation. Spheronization with a short retention time can help to reduce the amount of dust significantly.
The charge volume or weight (The quantity of product loaded into the spheronizer)
The optimum level depends upon the machine size and the product characteristics; there is an optimum quantity of product to be charged per batch into the spheronizer chamber that will produce the most narrow particle distribution and the best spheres. A typical charge volume for a machine with a 380 mm diameter disc is 4 kg depending upon the density of the material. Increasing the load per batch increases the hardness of the spheres and smooths the granule surface. With the larger 700 spheronizer a load of from 2 kg to about 12 kg is normal.
Product Parameters
The result obtained in the spheronizer depends on the physical properties and in particular the rheology of the product (rheology can be easily investigated using a Caleva Mixer Torque Rheometer - MTR). The particles must have enough pliability to allow deformation under the impact they receive during the process, but also must be strong enough to withstand the collisions with the friction plate, each other and bowl wall without being broken up and destroyed.
Rheology
The rheology of the product can be changed by using binders or lubricants, or by changing the mixing time and by altering the liquid content of the mix. Although the examination of the rheology of the product seems complex and potentially time consuming to perfect, with a Caleva Mixer Torque Rheometer (MTR) the ideal formulation can be determined very quickly and easily (for more information about the MTR and how it can be used contact your local distributor or Caleva info@caleva.com).
Binders can be used to increase the strength of the granules and reduce the amount of fine dust generated during spheronization. If too much binder is added and the granules become too hard, it will be difficult to obtain good spheres.
Lubricants will increase the plasticity but may also increase the amount of fine dust generated during spheronization.
Water can also be used as a lubricant. If too much water is used, sticking can occur on the friction plate and bowl wall. It can also happen that the granules will stick together, forming big lumps. If the extrudates are too dry, a high amount of fine dust will be generated. The optimum moisture content for spheronization is slightly less than for extrusion only.
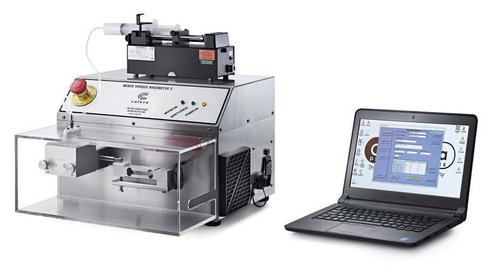
Auxiliary beneficial options for spheronizer configuration Drum Heating/Cooling Jacket
Heating or cooling water can be introduced in a jacket around the spheronizer bowl. Warm water can be particularly useful on the chamber wall to drive off moisture that would cause product to stick to the wall. Cooling the wall will avoid temperature rises in heat sensitive products, although the average temperature rise in a spheronizer is generally rather small (approximately 2 to 3 °C).
Air introduction (Fines air)
A slight flow of air can be introduced in the chamber from under the friction plate. This not only prevents dust from getting between the rotating plate and the wall of the chamber but also can help to remove moisture from the granule’s surface, improving the friction forces and process efficiency.
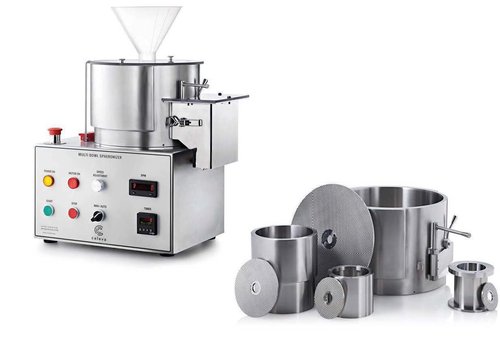
Automatic timer
It is useful but not essential to have an automatic timer on a spheronizer. Spheronization is a batch process and not a continuous process. Proper timing of the spheronization run time for each batch will help to maintain standard operating procedures and enhance performance standardization and product quality.
Non-Stick Coatings
For some products, the chamber wall and the plate can be coated with non-stick materials if this is necessary for ease of use with sticky materials or cleaning.
THE BENCH-TOP CALEVA MULTI LAB
The Caleva Multi Lab (CML) is a bench top apparatus that contains a mixer/granulator, extruder and spheronizer designed to work with small batches of material. Trials can be made covering the three initial steps of spheronization quickly, easily and with minimum use of experimental materials. The mixer has two configurations, one for standard products and one for products with a higher viscosity (these are generally products used in the petrochemical and catalyst industries. Reduced size bowls are also available being more suitable for working with smaller batches.
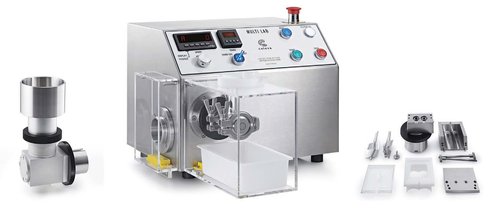
THE CALEVA MINI COATER DRYER
The Caleva Mini Coater Dryer (MCD) is designed to coat small quantities of pellets or tablets in laboratory development situations. It will effectively coat from a single tablet to a batch of pellets produced by the Caleve Multi-lab (CML) or other small extruder and spheronizer combinations.
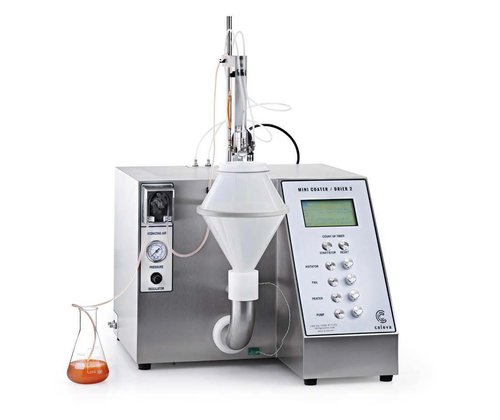
Together these two laboratory pieces of equipment make up an ideal combination covering all aspects of small pellet (0.5 to 3.0 mm) development.
THE CALEVA PRODUCTION SPHERONIZER 700 AND THE CALEVA VARIABLE DENSITY TWIN SCREW EXTRUDER
Working together these two pieces of Caleva production equipment make up an ideal combination covering all aspects of variable density extrusion and high quality pellet manufacture.
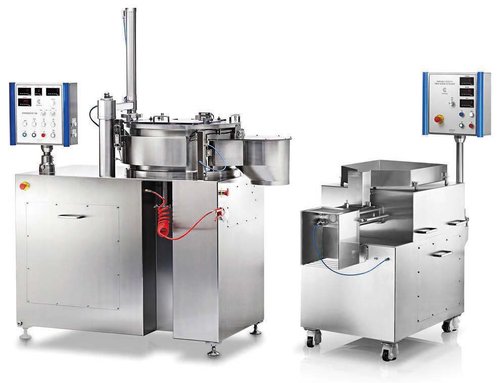