Continuous processes offer pharmaceutical companies a number of advantages. For example, they enable continuous quality control during production and a deeper understanding of the interdependencies between individual production steps. They also allow rapid intervention in the event of faults or process deviations, without the need to discard an entire batch. During the product development phases, tests can be conducted inline, eliminating the need for any subsequent scale-up - saving time during product approval process. There are many good reasons to consider continuous process technologies.
In general, there are three different types of processes: direct compression, wet granulation, and dry granulation. The choice of process depends on the compressibility and other properties of the ingredients.
Direct compression: simple and effective
Direct compression is an option if the blend of dry ingredients can be compacted immediately without needing to be granulated. In this case, the ingredients are channeled via feeders into the mixer and then directly into the tablet press. Following elastic recovery, the final coating is applied if necessary. This closed process is ideal for hygroscopic materials, as no moisture is introduced by the addition of air. This process saves a great deal of space and requires only a minimum of material logistics. There are also no process stops that could facilitate segregation of different sized particles.
In any type of process, continuous control using process analytical technology (PAT) is important. Near-infrared spectroscopy (NIR) is considered the first choice upstream of the tablet press. It screens the ingredients, providing a chemical fingerprint for each compound. The granulation moisture and active ingredient concentration can therefore be monitored in real time, and tablets can be rejected immediately if deviations are detected. Appropriate parameter adjustments can be made if necessary.
WET GRANULATION: GRANULATION EXTENDS THE RANGE OF CONTINUOUS APPLICATIONS
Wet granulation involves the use of very effective liquid binders that can be metered extremely sparingly. Compressibility and particle size distribution can therefore be accurately controlled. However, the process is quite complex compared to direct compression and dry granulation. A twin-screw granulator, such as the QbCon®1, an L.B. BOHLE R&D system that can simultaneously feed, granulate and dry, is used after mixing. Featuring short residence time and residence time distribution in the dryer, this device ensures that defective products are specifically removed. At the same time, that makes ingredient traceability easier.
At this stage of the process, NIR provides the option of monitoring content and particle sizes inline. Dust generation during drying is the biggest technical challenge in wet granulation. L.B. Bohle technology features special filters that ensure dust removal from the dryer, and the fine dust is returned to the process. This method is particularly safe, especially if high-containment processes (OEB 4 and 5) are involved.
DRY GRANULATION: BEST CHOICE FOR LARGE VOLUME, MOISTURE- OR TEMPERATURE-SENSITIVE INGREDIENTS
A dry granulation process requires less space and less energy input than wet granulation. However, processing using a roller compactor requires significantly more excipients than wet granulation - in some cases they account for as much as 40 percent of the tablet mass. The reason for this is that liquid binders are much more effective than powders. Nevertheless, dry granulation may be the best choice for some compounds in terms of product properties such as disintegration, tensile strength, compressibility, and particle size distribution. This applies particularly frequently to high-volume, moisture- or temperature-sensitive ingredients. In this process, the ingredients are channeled after mixing into an L.B. BOHLE roller compactor, which operates continuously, similar to a tablet press. The roller compactor compresses the powder thin ribbons. These are in turn milled into granules of the desired particle size distribution. Here too, NIR can be used for particle size measurement and control.
TABLET PRESS: A CONSTANT IN THE PROCESS
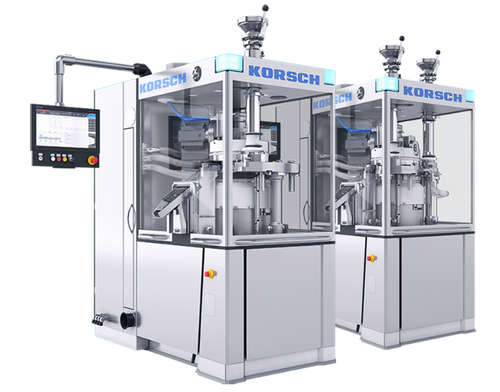
Be it direct compression or granulation - a tablet press is used downstream in the process. Based on the typical output of a continuous line, the KORSCH X 3 Tablet Press is particularly well suited for the application. This mid-sized tablet press offers a wide range of turret configurations and high containment flexibility. It also incorporates the most advanced production control system, which features an open architecture that allows it to be integrated easily into a centralized network including domain authentication, centralized formulation management, and centralized production report archiving. Innovative punch lubrication and dust extraction systems enable the X 3 to operate for particularly long periods without intervention This ensures optimal performance in the context of a continuous production line.
The author
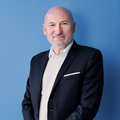