Developing a solid-dose nutraceutical product into a formulation that can then be compressed in a modern tablet press at high speed can cause technical challenges. Tablets are one of the most successful forms of administering medicines, and also offer an efficient means of reducing powders and granules into a compact product. The tablet is versatile, small, robust and accurate, and can be consistently mass produced at high speeds.
The problem of producing solid-dose nutraceuticals has to be explored as the industry progresses toward stricter regulations and higher standards, which are, in some ways, identical to those used for the pharmaceutical industry. Many of the most common multivitamin formulas contain up to 50 active ingredients and two to eight excipients, including coating ingredients. Pharmaceutical formulations tend to contain one to four actives and five to six excipients. These higher numbers of active ingredients in nutraceutical formulations bring challenges related to particle size, flow, compressibility, moisture sensitivity, ingredient interaction, content uniformity and quality control (QC) testing. For example, some active ingredients may be available in granular form, while others may be available only in fine powder form; some may be hydrophilic and others hydrophobic. Because of this, the ingredient blend may have many different particle sizes and ingredients with a variety of characteristics.
Ingredient blends can also have separation and flow issues. Tablet production from these blends can result in capping, sticking and different patterns on the faces of tablets during compression, as well as basic content uniformity problems.
Natural ingredients
Tablets are produced using punches and dies in a tablet pressing machine, wherein the ingredients of the product – usually in powder or granule form – are bonded into a solid shape by compaction at high forces. This technology has been used for many years in the production of pharmaceutical tablets to deliver drugs and medicines. Because of its reliability, this process has also been adopted for the production of some confectionery items, as well as other compacted products such as detergent tablets, sterilising tablets, cosmetics, catalysts and chemicals, in addition to nutraceuticals. However, as mentioned, this brings its own challenges.
The addition of natural ingredients in nutraceuticals – which have a tendency to be unrefined, abrasive, corrosive and hard – results in the components used to process them being subjected to damage. Tablet punches and dies are the main components that interface with the powders and granules and, as such, have to be robust – both metallurgically and in terms of design – in order to withstand the rigours of compacting nutraceuticals.
Vitamin, mineral and food supplement tablets tend to be quite large and bulky when compared with pharmaceutical tablets, especially multivitamins. This is to enable sufficient delivery of the beneficial ingredients. They often require high compaction forces to bond the ingredients into a robust tablet, and the tableting equipment is usually run at high speeds for long periods of time to satisfy the nutraceutical industry's demands for high output and low cost.
Balance of excipients
Nutraceutical formulations normally have more actives present in higher weight than pharmaceutical formulas. The limits of dose size typically result in restricted room for excipients. The typical nutraceutical formulation has 70-90 per cent actives with the balance as excipients, while traditional pharmaceutical formulation has 70-90 per cent excipients and 10-30 per cent actives.
The fewer excipients and variety of actives in the same formulation make it difficult to achieve certain desired outcomes, such as disintegration time, hardness and friability. Nutraceutical customers are also demanding smaller dosage size and fewer ‘other ingredients’, which narrows the options for formulators. As the choice of excipients gets narrower, it becomes more difficult to formulate and achieve the required result for the product.
Product design
When developing a nutraceutical product, the formulator is faced with the challenge of delivering the correct quantity of each ingredient into every tablet or capsule. Non-uniform powder flow can negatively affect the distribution of active ingredients from tablet to tablet or capsule to capsule, and cause failure to meet active ingredient claims. Poor compressibility can introduce productivity problems in the tableting process. Attention to the production process and the use of high-quality punches and dies (with or without specific anti-wear, anti-stick and anti-corrosion coatings) can prevent time-consuming and frustrating trial-and-error resolution of problems in the finished product.
Something else to consider is the identification and marketing of the brand. Apart from the packaging, the tablet shape and inscription is often utilised for brand identity and marketing, including shapes and forms, plus inscriptions such as logos, product names or codes. Adding to the challenge, many nutraceutical tablets tend to be produced using neutral colours such as browns and greys with mottled, textured or granular appearances, which can make any embossing difficult to read.
Careful design of the tablet shape and form, and the force applied during compression, needs to be considered when choosing suitable tooling. It is advisable to avoid small, delicate and complex shapes with vulnerable, high-stress areas.
Tooling construction
As well as good design, equal consideration must be given to the selection of materials for the tooling construction. Because of the aggressive nature of some nutraceutical ingredients, the properties of materials are extremely important, and must be balanced to give optimum tooling performance and durability. These properties include abrasion and corrosion resistance, compressive strength, hardness and toughness, and also resistance to chipping and cracking.
Tooling has to have a long life, and be anti abrasive and wear-resistant. To achieve this, several options are available.
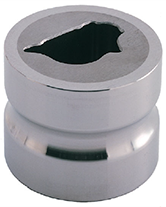
Raw material
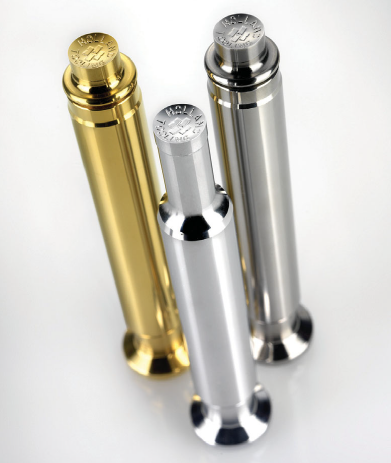
Due to the nature of nutraceutical ingredients, wear and degradation of the tooling will lead to other tabletmaking problems, such as adherence of the granules because of the pitted and worn surfaces of the punches, as well as 'capping' or 'lamination' of the tablets – which could prove costly for the nutraceutical manufacturer.
The correct choice of material will help to reduce the risk of damage to the punches and dies from the effects of abrasion, corrosion and impregnation of hard granules. There are thousands of steel types available, yet only a few meet the complex design and functional requirements necessary for tablet tooling. Alternative materials, such as tungsten carbide, and enhancement coatings and treatments should be considered. Commonly used materials for nutraceutical tooling include high carbon, high chrome, cold work tool steels.
Tungsten carbide is often used for the dies to prevent wear and deformation of the die bores. It features a high compressive strength with an extremely high wear resistance. This helps to reduce die bore wear and ringing, and lasts longer than conventional die steels. Tungsten carbide is not always a preferred solution; an alternative material suitable for compressing abrasive formulations would be HPGMD, a specialist powder metallurgy grade steel.
Coatings
When coatings are developed correctly, and their beneficial characteristics are matched to those of the formulation, they can help to increase corrosion resistance, wear resistance and prevent sticky formulations adhering to the punch tip faces. Traditionally, the most popular coating used within the global tablet tooling industry is hard chromium, due to its low cost and general purpose characteristics in terms of average anti-stick, anti-corrosion and anti-wear properties. However, electroplated hard chromium has several disadvantages:
Hydrogen embrittlement
When hard chromium is applied to tooling, a certain amount of hydrogen penetrates the substrate, which decreases the steel’s strength. That is highly undesirable in a component subject to high cyclic loading. To counter this effect, the electro-plated tools undergo a baking process known as de-embrittlement that reduces, but does not totally eliminate, the unwanted characteristic. Indeed, tooling with hard chromium applied to it can only withstand a maximum of 80 per cent of the designed safe working load that could be applied to an uncoated tool.
Micro-cracking
Micro-cracks develop during the plating process when the internal stress exceeds the tensile strength of the chromium, which is hard and brittle. These micro-cracks are problematic because they provide a porous route to the substrate that will, over time, allow aggressive tablet formulas or cleaning solutions to attack the steel beneath the coating.
Environmental Issues
Hard chrome itself is not an environmental hazard, but there are problems associated with the plating process. The main issue is the chromic acid solution used as it generates a waste product that contains hexavalent chromium – a tightly controlled substance that must be disposed of correctly.
Targeted Technology
PharmaCote® EC is a chromium-rich coating that is applied via magnetronsputtered physical vapour deposition. In contrast to other techniques, with magnetron sputtering, the target material is vapourised by exciting the target chromium atoms with a bombardment of gaseous particles. Magnets behind the target material assist in the process. The magnetron sputtering process causes a very smooth (anti-stick) and dense coating to form, and the process incurs none of the drawbacks associated with applying hard chrome.
Another specific coating that has been developed to combat problems in the manufacture of nutraceuticals is PharmaCote® Resilient Surface (RS). Abrasion is a major problem in nutraceutical tablet manufacture; products often contain high quantities of hard, abrasive, sharp-edged minerals that, when repeatedly compressed, can scrape away or penetrate the surface of the tool. This can lead to the erosion of punch tip detail, such as logo embossing and other identification. Eventually, this wear can lead to weight variation, sticking and other issues resulting in the scrapping of the punch.
This RS coating is applied with electron beam technology, allowing a very hard coating to be applied, while still giving a smooth finish. One of the reasons for this coating’s strong wear resistance is its high hardness value (3,000HV). This coating is only applied to the punch tip as it could cause damage or wear to the tablet press if the whole punch was coated; the compression rollers have a much lower hardness.
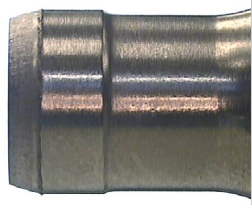
Case study: anti-abrasive coating
In January 2008, a leading nutraceutical manufacturer was experiencing serious issues with a particularly abrasive formulation of part of its range of vitamins. Many nutraceutical products can be abrasive in nature, but this particular compound was causing extreme difficulty. Only 22 million tablets were able to be compressed before the tooling was worn to such an extent that it was deemed to be unserviceable. This not only necessitated the purchase of new punches, but also incurred the associated downtime inherent with replacing and setting up 37 stations of tooling. I Holland was challenged to find a solution to extend the life of this tooling. Through its continual R&D programme, I Holland was in the final stages of developing a promising new anti-abrasive coating: RS. This formulation presented an ideal opportunity to trial the product.
Trial set-up
A compression trial was set up at the customer’s premises using stations of RS-coated punches. A camera system was also installed to enable comparisons to be made during the trial. The goal was to see just how far the useful life of the tooling could be extended by the use of a coating. The RS coating was tested with the same abrasive formula against HPG-P and a competitor's coating. When the results started to take shape, the disparity between the two products was clear. The competitor's coating was shown to fail between 19.5-21.1 million tablets – the premium steel was withdrawn between 21.1-22.8 million tablets – but the RS coating was still serviceable at 44,010,000 tablets. This represents an approximate 93 per cent increase in the lifespan of the tooling when compressing this formulation.
The benefits
These results translate into valuable cost savings and productivity increases for the customer. RS-coated tooling demonstrated that it can last nearly twice as long before it requires replacement, with longer run-time and less need for costly downtime due to tooling replacement. In addition, product yield will also increase as the presses need to be set up fewer times.
Summary
The development of solid-dose nutraceutical products into a formulation that can be compressed in a modern tablet press to a tablet form, with both speed and quantity, can be a complex and problematic procedure. With certain considerations and measures in place, it can be achieved successfully. As nutraceutical formulations nearly always have more actives present in a higher weight than pharmaceutical formulas, the room for excipients is restricted, making it harder to formulate. Consideration must also be given to delivering the correct quantity of each ingredient, in each tablet. This can cause failure to meet active ingredient claims. This is where choosing the correct tooling comes into its own. By selecting the right quality punches and dies, problems during manufacture can be prevented. Today, in order to produce robust tablets with tailor-made properties, detailed design of nutraceutical tablets is essential. Tablet manufacturers should not overlook design because it is key to the quality of the end product. Good tablet design is extremely important, as it has an impact upon anti-counterfeiting, tooling strength, coating of tablets, durability and functionality. It also helps avoid tablet sticking, picking, lamination, capping or premature tooling failures right at the beginning of the process, by ensuring a problem-free end product – getting all these factors right is imperative to a ‘good’ tablet. The process is something that should not be rushed; it needs to be well thought out and considered, as good tablet design is essential to prevent downstream problems, produce high-quality tablets, and maximise the efficiency of the tableting process. All these factors are important considerations to overcome problematic production issues in the manufacture of nutraceuticals, and should be explored from the initial conception of a tablet.
About the authors

Since joining I Holland in 2003, Rob Blanchard – Research, Development and Quality Systems Manager – has been instrumental in the development of the company’s PharmaCote® range of surface treatments and coatings for tablet compression tooling, designed to improve properties such as wear resistance, corrosion resistance and anti-stick characteristics. He is part of the Eurostandard steering committee and responsible for I Holland’s registration to ISO 9001:2008. Rob also coordinates I Holland’s close collaboration with various respectedacademic research bodies.
Email: rob.blanchard@iholland.co.uk
Trevor Higgins is I Holland’s longest serving employee, having joined the company in 1969 as its first apprentice. He has worked in all areas of manufacturing and technical support, and was appointed Director of Production in 1984 and Technical Director in 1991. Trevor’s current position is Technical Expert – he delivers seminars and presentations worldwide and provides direct support to customers on production issues.
Additionally, Trevor is the creator of the Eurostandard (a global standard for European tablet tooling) and has served on the Tableting Specification Manual (TSM – the US tablet tooling standard) committee for over 25 years.
Email: trevor.higgins@iholland.co.uk
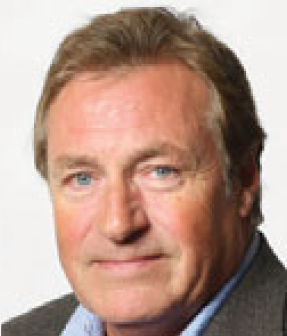