STYL'One Evo, a versatile tool
Compression force, speed, dwell time: Every parameter in the tableting process is variable, but crucial. The French team is gaining access to the kinematic factors in two interlinked ways: experimentally and numerically (see box for details). In the second approach, the compression processes are modelled mathematically. Vincent Mazel is also planning to develop a digital twin that simulates the behaviour of the powder, allowing the researchers to collect information about the process-related stress on the tablet.
The numerical results are systematically compared with those of the experimental laboratory tests. These are being carried out on the STYL’One Evo compaction simulator from MEDELPHARM and on rotary tablet press. The former is a special “2-in-1 tool” in this project, according to the scientist. In order to understand tablet properties and defects, the STYL’One Evo makes it possible to “play with the compression kinematics and foresee their effects on the rotary press.” Also, the instrumented device can use its force and displacement sensors to characterise the compaction behaviour of the powder and thus generate important parameters for numerical modelling.
STRAP, from compaction simulators to rotary tablet press
The expertise and methologies developed by the University of Bordeaux will be applied, in collaboration with TU Braunschweig, in a new research project named “STRAP” (see info box on p. 14/15). The Agence Nationale de la Recherche (ANR) and the German Research Foundation (DFG) are funding this research until 2026 in order to promote Franco-German research projects. The project is of interest, because “this topic has never been investigated before”, says Vincent Mazel, who is delighted to be working with the German team to explore the effects of changing formulations on the overall tableting process.
A decade of successful collaborations
The collaboration between the I2M Institute and MEDELPHARM is well established; Vincent Mazel is a long-standing and versatile user of MEDELPHARM equipment: the institute has been using the STYLCAM, the first mechanical compaction simulator from MEDELPHARM, since 2011. He still uses the device, preferably for demonstrations and training purposes, because “its mechanical functions make the basics understandable.” Not long
after, in 2013, the successor model, the STYL’One Evo, was added – back then still as a prototype, now replaced by the latest version. It is used for research purposes “that delve deep into the technology,” Vincent Mazel explains, emphasising that this flexibility is only made possible by the support of the MEDELPHARM colleagues: “We make advances together by exchanging information on the software, discussing the die-wall sensors or giving each other feedback on the process activities.”
Scientific publications: a tool for education & technology development
This exchange also furthers the companies’ own understanding of the pharmaceutical product lines: Dr Friederike Gütter, process specialist at KORSCH’s INNOVATION CENTER, uses the data and publications from I2M “in the internal training of our mechanical engineers, ensuring that knowledge about the tablet and it compaction flows into device development.” And Bruno Leclerq, coordinator of the KORSCH INNOVATION CENTER and MEDELPHARM Science Lab, integrates the institute’s scientific findings into customer consultations, so that “some have been referring to I2M publications for years”. In his view, it is therefore thanks to the I2M researcher that the STYL´One concept is in such widespread use: “The market for compaction simulators used to be small; only a few companies used them. Vincent Mazel has had a major influence on our market developments.” For Gütter, the larger rotary presses available at the KORSCH INNOVATION CENTER are an opportunity to offer I2M a special research advantage: “The path from development to end product, from the idea to testing on a rotary press, is quick and easy with us.”
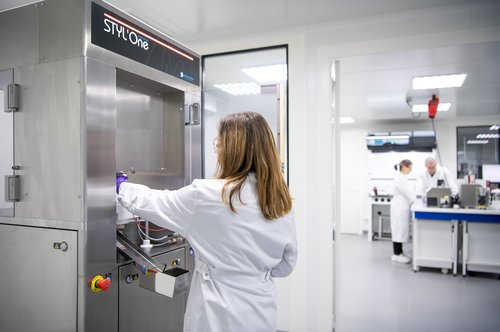
The “STRAP” Project - Scale TRAnsfer in Pharmaceutical compression – from compaction simulators to rotary presses
The project is being carried out as a cooperation between the Institute for Particle Technology (iPAT) at the Technical University of Braunschweig and the Institut Mécanique et d’Ingénierie (I2M) at the University of Bordeaux. The project is managed by Dr Jan Hendrik Finke in Braunschweig and
Dr Vincent Mazel in Bordeaux. STRAP investigates the effects of different formulations on the overall process on the Styl’One Evo compaction simulator and the XL 100.
To this end, the Franco-German team is focusing on the two quality-determining sub-processes “filling” and “compacting” on rotary presses. The iPAT is researching the material behavior during die filling on the compacting simulator and its transfer to the rotary press, while the I2M is focusing on the compaction process and the reproducibility of tableting errors.
After the separate analyses, the results are correlated in order to derive a reliable prediction of process parameters and correlated product properties on industrial machine scales.
The Institut de Mécanique et d’Ingénierie (I2M)
The University of Bordeaux focuses on the deconstruction and reconstruction of mechanics. Around 340 employees take a multidisciplinary look at interactions – physical and physico-chemical – between manufacturing processes and materials. The team led by Dr Vincent Mazel investigates the problems that arise in connection with pharmaceutical powders and their processing steps.
About the author
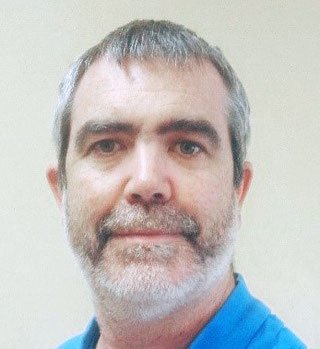
Vincent Mazel received his doctorate in physics and materials chemistry in 2006. From 2008 to 2014, he was a lecturer at the University of Paris Sud, and since 2014 he has held a professorship at the Institut de Mécanique et d‘Ingénierie at the University of Bordeaux.