Why does sticking occur?
There is no simple answer to this question. It can be due to any number of reasons,from the physiochemical properties of the formulation to the surface characteristics of the punch face. It can also be related to the machinery, for example the compression force and speed, as well as the enviromental conditions like temperature and humidity.
Sticky granule: Problem
The granule formulation can be highly influential when it comes to sticking. Simply put, sticking is the battle between the cohesive forces holding a tablet together and the adhesive forces between the ingredients in the formulation. When the difference in force is significant and adhesive forces are higher, sticking occurs.
There are three factors to consider when understanding the cohesive forces. The first is Van der Waals. This is the attraction of intermolecular forces between molecules and is affected by surface roughness and the effective contact area. Essentially, molecules can attract each other at moderate distances and repel at close range. Although these forces are very small, in mass they combine not only increasing cohesive forces within a tablet but also creating adhesive forces (when interacting with the elements in the tools steel or coating), which can then be a cause of sticking.
Capillary action is the second cohesive force created when moisture condenses into the gap between a particle and the surface, causing a capillary bridge. The strength of these forces can depend upon relative humidity, gap geometry and the surface chemical condition.
Capillary bridges increase the cohesive forces that bind a tablet together, and like Van der Waals, they can also be detrimental by increasing the adhesion forces between the granule and the punch tip faces, causing sticking. This is why it’s important to control the environment in all areas of tablet production and reduce humidity.
The third cohesive force is electrostatic. This is when tribo-charging occurs between contacting materials. It forms static electricity and is evident when granule is very dry. The resulting force can be fairly strong and long-ranged, creating cohesive and adhesive forces.
The environment is the biggest influence on adhesive forces causing sticking between the formulation and punch tip faces. Temperature can affect some active pharmaceutical ingredients (APIs). A good example of this is Ibuprofen, which has a very low melting point. For this reason, it is important to control the temperature in any area where the tabletting process takes place. Maintaining the temperature at a low level will reduce sticking problems.
Humidity is also a potential problem.
Moisture within a tablet can strengthen the adhesive force. This occurs with an increase in capillary action between the tooling surface and the granule. Capillary bridges form, causing high adhesion areas, creating sticking. Moisture can enter the process during wet granulation or from excess humidity in the compression chamber in a non-environmentally controlled area – the latter can even affect direct compression formulations.
Sticky granule: Solution
Overcoming sticky granule can be a complex task. A good starting point is to optimise the enviroment in which tablet compression takes place and areas where tooling and granule are stored with the correct temperature and humidity controls.
Consider your tablet tool coating. Choosing an anti-stick coating is essential as conductive or non-conductive tool coatings or treatments can also influence cohesive and adhesive forces.
Specialised punch and die coatings can have a huge impact on the productivity of tablet manufacture. When used in conjunction with high-quality tooling steel, they allow for better tableting efficiency and output.
Surface finish: Problem
The morphology or surface roughness of a punch tip can affect tablet production. While there is the perception that polishing the punch tip face to a mirror finish will prevent sticking, this is not the case. Research on the interaction of different surface textures has shown that the standard specification for tablet punch tip faces can include a range of surfaces, which interact with formulations in different ways.
The required standard surface for a punch tip is between 0.1 to 0.025Ra (roughness average). This variance can have a huge effect on sticking. Each coating’s surface condition works differently because of the surface roughness. In order to prevent sticking, it’s important to understand the effect on the interaction between the granule and the surface finish.
Surface finish: Solution
The punch surface can be determined in a number of ways such as:
- Measuring the surface roughness after polishing using optical surface profilometry
- Using scanning electron microscopy to study the structure of the steels and coatings
- Measuring the adhesion forces in order to create a nanoscale map of the surface
By investigating the surface condition, the correct coating can be applied.
Tool maintenance should also be addressed. Assessing and polishing tooling are crucial steps to ensure that any tooling defects can be dealt with early. Automated polishing using a MF polishing machine is the best method to ensure a suitable surface will be maintained. This also repairs small areas of damage and abrasion that occur during production. By restoring the optimum finish of the tooling, problems like sticking or picking can be prevented.
Poor tablet design: Problem
Insufficient tablet compaction is another cause of sticking. In a tablet with decreased hardness, the cohesive force can be less than the adhesive force to the tooling surface. This is a common problem with effervescent tablets as they require a lower hardness to help increase the dissolution rate.
Tablet design also has an influence on sticking. A typical indicator is when sticking is found around a tablet’s core. However, it can occur in other parts of the tablet as well.
The principal reason for insufficient tablet compaction is an uneven distribution of compaction forces across the tablet. This is usually due to the shape of the tablet and how concave it is. With a concave tablet profile, the core can be lower in hardness, causing sticking to the centre of the punch face. This occurs because a concave punch tip profile compresses the formulation around the edge of the tablet more than in the centre due to the tablet profile.
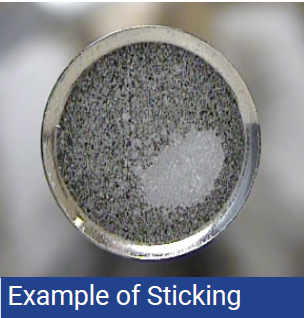
Poor tablet design: Solution
The eXtended Dwell Flat (XDF) head design is one way to increase the dwell time, helping the granule to consolidate during compaction without automatically increasing tablet hardness. Adding either a coating or a polymer insert will also help to reduce the adhesive force.
A tablet design with a flatter profile and changing from a deep single radius to a double radius, reduces the soft area in the centre of the tablet with the lowest cohesive force. This results in an even tablet hardness, helping to decrease sticking issues by increasing the cohesive forces.
Changing the profile to a double radius can also be beneficial because an even coating thickness is easier to achieve and branding or required markings like breaklines can be accommodated.