The challenge
I Holland has recently helped Thompson & Capper to make major cost savings on the manufacture of one of their siliceous earth products. The tablets compressed well during the development phase, but it was not until the tablet hit full scale production that it became clear the formulation was extremely abrasive. The first batch produced only 1.5 million tablets on the Manesty D4, 20 station machine, and wear on the punch tips was visible when de-tooling the press. Only 4.5 million tablets were produced per tool set which is far below output levels expected for typical formulations, where tablet output per set would be in the region of 50-60 million tablets.
The initial tools supplied were on I Holland’s standard steel HPG-S (Holland PharmaGrade® Standard). After Thompson & Capper ran three sets, it was obvious to I Holland that a more sophisticated, wear resistant solution was required. Working with the I Holland Customer Support Group it was agreed to run a set of punches with I Holland’s NutraTool™ , manufacturered from a very hard wearing ESR NutraGrade™ steel and prepared with NutraCote™, an extremely wear resistant coating. A full set was supplied and after producing 35 million tablets, they were still in a useable condition. Operators in Thompson & Capper’s production team inspected the condition of the tool set daily, and it was finally agreed to remove the coated tools at 45 million tablets.
According to Kevin Fairhurst, Production Manager at Thompson & Capper, they were surprised by the results: “We were completely astounded by the increase in tablet output on just one set of tooling. Despite an increase in the cost of the tooling for the coated set, we were able to increase output per set by 10 times. Even then, the decision to stop production at that point was based on wear to the compression rollers, rather than tip wear. More significantly, we were able to save on 9 tool changes per set. One tool change taking a whole production shift.”
Thompson and Capper has now purchased further sets of NutraTool™ tooling and is looking to roll it out to other abrasive products as their portfolio expands. They are also considering other solutions from I Holland’s PharmaCote® range for their sticky formulations and will be using the TSAR≈ Predict service to facilitate selection of the right coating for these.
Total increase in cost of tooling = 78%
Total increase in tablet output = 900%
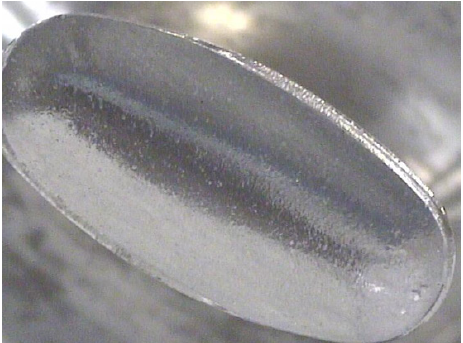
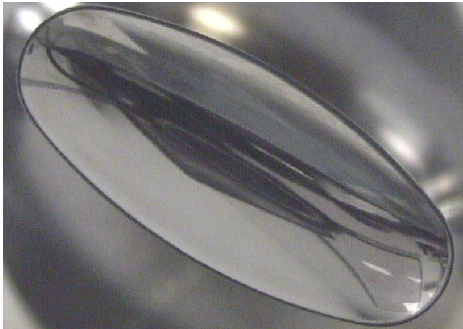
NutraCote™
Discription: A distinctive silver blue coloured coating applied to the tip of the punch, with superb wear resistant properties, but also good resistance to corrosion.
Features: Very smooth finish
Thickness: 2-4 microns
Hardness: 3000Hv (est)
Benefits: A very wear resistant coating due to the very hard surface layer, more than 3 times the hardness of Hard Chrome. Extremely easy to clean and maintain using an ultrasonic bath and light automated polishing.
Application: Applied to NutraGrade™ steel. Punch tip only coating - to prevent excessive wear on compression rollers.