Comprehensive review of modern techniques of granulation in pharmaceutical solid dosage forms
The review provides an extensive overview of granulation techniques in pharmaceutical manufacturing, comparing traditional and modern methods. It details dry granulation techniques such as slugging, roller compaction, and pneumatic dry granulation, emphasizing their methods, benefits, limitations, and uses. Wet granulation is also explored, covering eleven techniques including high-shear, low-shear, fluidized bed, and steam granulation, among others. Each technique is analyzed for its processing steps, advantages, and drawbacks, aimed at improving pharmaceutical formulations.
*Granulation involves creating granules from powder to enhance drug quality by improving handling, preventing dust, and optimizing functionality. Key processes include wetting, coalescence, consolidation, and attrition. Techniques are chosen based on drug properties, excipients, and desired outcomes.
*Dry granulation is moisture-free and prevents degradation in sensitive drugs. Methods like slugging and roll compaction are discussed in detail. Pneumatic Dry Granulation (PDG), a newer method, combines roller compaction with air classification to produce granules with excellent flow and compressibility, addressing the challenges faced by moisture and heat-sensitive drugs.
The review serves as a comprehensive guide for researchers, professionals, and students in understanding and selecting appropriate granulation techniques for pharmaceutical development and manufacturing.
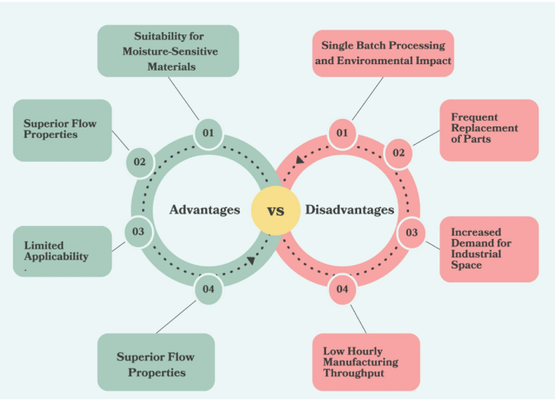
Comments
No comments posted yet.