Capping refers to the separation of the top or bottom from the body of the tablet. Instead of a biconvex tablet you end up with a mix of very rough, underweight, “flat”-faced tablets and fragments of the detached convex portions. Laminar failure may also occur in the body of the tablet which, if not immediately visible, is often revealed on hardness or friability testing. Lamination refers to a horizontal or radial failure plane, normal to the axial (topbottom) axis, the axis of compression. Why are such tablet failures horizontal and why are they dependent on the speed of tablet production?
The answer is rheological. Although more commonly associated with liquids and semi-solids understanding the flow and deformation of your compression mix under pressure is essential for designing a robust tablet which can be manufactured at commercial scale.
VISCOELASTICITY MEANS SPEED SENSITIVITY
Elasticity is the ability of a solid to return to its original shape and size after the deforming force is removed. Deformation is immediate, and proportional to the applied force. Elasticity is obviously an undesirable attribute of a compression mix.
Plasticity is a desirable attribute for tableting where the deformation is permanent, and the compressed particles will not resume their original shape and size after the deforming force is removed. Plastic or ductile materials permanently deform under pressure but require time to flow, maximizing interparticle bonding area. This introduces time-dependency/speed-sensitivity. As tableting speed increases the time under pressure (dwell time) decreases.
In practice, compression mixes and their components show a mixture of both properties and are described as viscoelastic. At slow speeds, the dwell time is long enough to allow flow and plastic (permanent) deformation, which outweighs the negative effects of elastic recovery. At higher speeds, the shorter dwell time may be insufficient to allow enough plastic deformation to overcome the timeindependent elastic effects. The elastic effects, which were always present, therefore become more significant at shorter timescales.
The time-dependency/speedsensitivity of viscoelastic compression mixes is further complicated by post-compression relaxation where the elastic effects initially countered by plastic deformation set up stresses within the tablet which gradually dissipate by axial relaxation.
Microcrystalline cellulose is the most compactible plastic/ductile direct compression filler-binder but shows more speed sensitivity and relaxation effects than the less compactible alternatives such as lactose or dicalcium phosphate. Brittle fracture of lactose is often relied upon to counter lubricant sensitivity by exposing fresh bonding area on compaction, but this may also introduce a new speed sensitivity if there is insufficient time at higher speeds to allow rearrangement of the fresh fragments beyond the confines of the original particle.
Viscoelasticity of the compression mix therefore explains the time (speed) dependency of capping/lamination but why the characteristic horizontal/axial failure planes? The answer is that the axial compression timescale (dwell time) is shorter than the radial compression timescale due to the retaining effect of the die-wall, from tablet formation until ejection. Axial relaxation is immediate as soon as the upper punch starts to withdraw, but the tablet cannot relax in the radial direction as it is constrained by the die wall until ejection. The ratio of plastic to elastic effects will therefore be greater in the radial axis and immediate relaxation can only take place in the axial direction. Otherwise known as anisotropic nonequilibrium rheology.
Other time dependent contributors to capping and lamination include entrapped air and friction between the tablet and die. At slower speeds air can escape from the die. If entrapped air at higher speeds is of concern the use of tapered dies or precompression can be evaluated. Die wall friction will increase with pressure and speed. Excessive friction can cause added stress on tablet ejection so under-lubrication should be avoided. Minimizing lubricant levels to avoid problems during small-scale low-speed tablet development may predispose the formulation to capping/ lamination (and sticking) problems at large-scale high-speed Production. Regardless of other timedependent mechanisms, the speed sensitivity of the compression mix should be evaluated during development. Separately, the ability of compression mixes to flow and fill the dies at higher speeds must be assessed, as simulating high speed compaction profiles does not address feeding problems.
TABLET MACHINES
Tablet machines range from small-scale low-speed hydraulic presses, through single-punch eccentric machines, to multi-punch rotary presses of increasing turret diameters and speeds, used for large scale commercial tablet production.
With a simple hydraulic press, you can hold the material under pressure indefinitely, so dwell times are seconds to minutes, unrepresentative of the millisecond dwell times of rotary tablet machines. The ratio of plastic to elastic effects is maximized. The technique is material sparing but not predictive of higher speed tableting.
Single-punch eccentric presses are useful for smallscale manufacture but have a single-sided compression Speed Sensitivity Assessment is a key information. Low Viscoelasticity, low Axial relaxation & low wall friction are all essential in designing a robust tablet.(upper punch) to make tablets, while rotary presses use double-sided (upper and lower) compression. Single punch machines have minimal dwell times due to the instantaneous upper punch penetration and withdrawal. Rotary presses typically use flat punch heads which increases contact time with the roller, extending the dwell time.
Single punch machines typically produce less than 100 tabs/min whereas rotary machines with multiple tools can produce in the range 100 to 10000 tabs/min. 100g compression mix on a single punch machine will yield 1000 x 100mg tablets in 10 mins whereas 10kg would be required to run a large rotary press for 10 mins.
For rotary presses the larger the turret the greater the linear speed (tangential velocity) for a given rpm, values up to 1000mm/s being typical. As dwell time is essentially the contact time between the flat of the upper punch and the roller it can be calculated for a specific machine by dividing the flat diameter by the linear speed. The use of precompression has the effect of extending dwell time and facilitating deaeration.
Increasing the machine size going from development to Production is attractive but runs the risk of sudden failure if the increasing tableting speed exceeds the capability of the formulation. During development of the formulation there will probably not be sufficient material available to feed a large high-speed press. To evaluate high-speed performance without using excessive material requires a compaction simulator.
COMPACTION SIMULATION
A compaction simulator is usually a hydraulically or electro-mechanically actuated single punch press which can be programmed to reproduce the compaction profile of a particular tablet machine at multiple speeds. Because it is a single punch it is easy to use external lubrication to evaluate the effect of lubricant which often has a dominant effect on compactability.
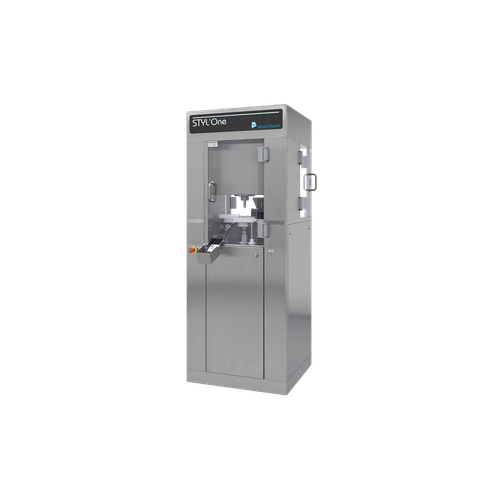
A typical compaction profile is a plot of hardness or tensile strength vs the applied force or pressure. Does the gradient of the profile decrease with increasing simulated speed of compaction? If so, is the compaction profile corresponding to the expected speed of commercial Production acceptable? If a plateau is seen is there capping, or laminar failure on hardness testing? Does the plateau occur at lower tensile strengths as the speed is increased? Is there a maximum pressure beyond which tableting is no longer possible and does this maximum pressure decrease with increasing speed?
Without a compaction simulator you will not know these answers until scale-up to commercial Production. If failure occurs during commercial production, it will be necessary to file a regulatory variation to improve high speed performance or else be stuck with a lower than desired output. Either way, a very expensive speeding ticket! Much better to evaluate high speed performance during development using compaction simulation when reformulation is still an acceptable choice.
It is much better to build in high-speed robustness during development using a compaction simulator. Evaluating the maximum tolerable level of lubricant is best done at high speed as it is the edge of failure at commercial speeds that decides lifecycle robustness not feasibility at low speed. The same applies to control of raw material or other changes during the product lifecycle.
QUALITY BY DESIGN REQUIRES COMPACTION SIMULATION
Compaction simulation allows small-scale materialsparing approaches to dealing with the inevitable speed sensitivities inherent in processing viscoelastic compression mixes. The alternative to Rheology is Theology… pray your formulation holds together, not a favored regulatory approach!
THE AUTHOR
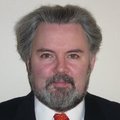