A cooled material flow from the material supply to the tablet
KORSCH, a leader in tableting technology, showcases its expertise in solving complex challenges through innovative, customer-driven solutions. In a recent project, the company successfully addressed the issue of compressing a powder with an exceptionally low melting point (Tmelt ≈ 6 °C). Achieving the required die table temperature (Tdie table max = 5 °C) demanded a comprehensive cooling strategy.
Key features of the solution included:
- Environmental Controls:
Production room maintained at 15 °C ± 1 °C and 50% ± 5% humidity
Compression material pre-cooled to 4 °C ± 1 °C
- Advanced Cooling Mechanisms:
Use of a cooling fluid at 2 °C ± 0.5 °C in separate circuits for the material feed, clamping plate, and turret
Insulated cooling jackets for material feeds and "cooling channels" in the turret and die table
- Simulation and Testing:
Computational Fluid Dynamics (CFD) simulations optimized the design to achieve a die table temperature of Tdie table < 4 °C
Prototypes confirmed consistent material flow temperatures below 5 °C without condensation or material melting
The resulting tablets met European Pharmacopeia 2.9.5 standards, affirming the system's efficacy. KORSCH’s tailored cooling solutions, from punch tip cooling to comprehensive system designs, underline its commitment to addressing heat challenges in tablet compression with precision and reliability
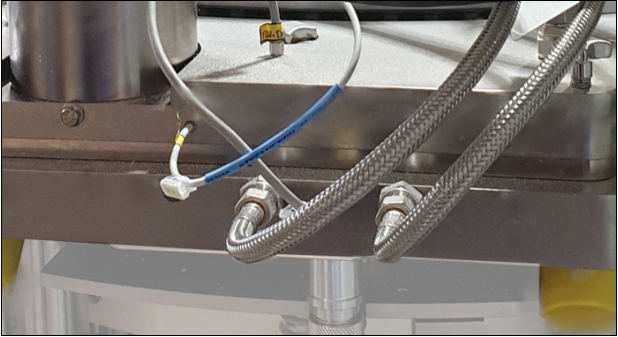
Comments
No comments posted yet.