Operational advantages of using hot melt extrusion to create amorphous solid dispersions
Oral drug delivery is a preferred method due to its convenience and high patient compliance. However, many modern drugs suffer from low solubility, resulting in poor bioavailability. To address this, drugs with low aqueous solubility, classified as BCS Class II and IV, benefit from the creation of amorphous solid dispersions (ASDs), which enhance solubility and bioavailability. ASDs are produced using technologies like spray drying and hot melt extrusion (HME), with HME offering several key advantages.
Spray Drying: Advantages and Limitations
Spray drying involves dissolving active pharmaceutical ingredients (APIs) with polymers in a solvent and converting the solution into a dry powder. The process is versatile but faces drawbacks:
- Complexity and Time: Often requires secondary drying, extending production timelines.
- Batch Processing: Inefficient compared to continuous manufacturing, with higher susceptibility to errors.
- Scalability Challenges: Equipment is bulky and difficult to scale.
- Process Variability: Thermodynamic and kinetic factors complicate defining and optimizing the process.
Hot Melt Extrusion (HME): An Efficient Alternative
HME uses heat and shear to mix powdered APIs with polymers, forming extrudates that can be processed into oral dosage forms. Key advantages include:
- Continuous Manufacturing: HME operates on a first-in, first-out basis, making it faster and more economical.
- No Solvents Required: Reduces environmental and safety concerns.
- Scalability: Compact equipment simplifies scaling from laboratory to commercial production.
- Ease of Process Control: HME processes are easier to define, with controllable parameters such as melt temperature and screw speed ensuring consistent quality.
Operational Benefits of HME
- Flexibility and Adaptability: Continuous production allows dynamic responses to market demands without the inefficiencies of batch production.
- Streamlined Scaling: HME facilitates smooth transitions from small-scale preclinical production to large-scale commercial manufacturing.
- Simplicity in Process Monitoring: Straightforward parameters like residence time and melt temperature enhance reproducibility and ease of process adaptation.
Conclusion
HME is a robust and flexible technology for ASD production, addressing solubility and bioavailability challenges while enabling efficient drug manufacturing. It offers additional benefits like taste masking, food effect reduction, and drug release modulation, making it a preferred choice for drug developers.
(Source: AbbVie, by Shantanu Sonparote)
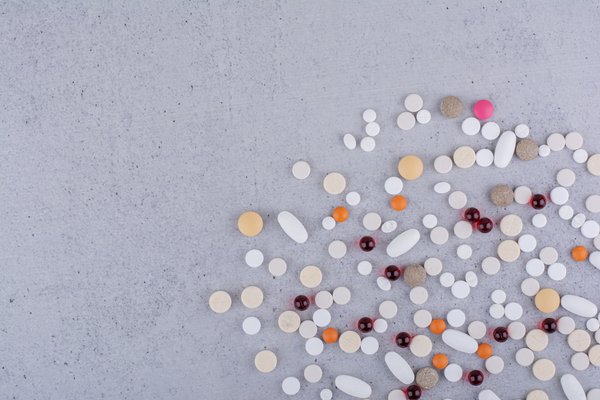
Comments
No comments posted yet.