Scientific papers
This study explores the impact of incorporating viscoelastic behavior in finite element method (FEM) modeling during die compaction of pharmaceutical products and its potential to enhance the correlation between experimental and simulated compression curves. The modeling was carried out on a pharmaceutical excipient, microcrystalline cellulose (MCC), utilizing the Drucker–Prager cap model coupled with creep behavior in Abaqus® software. Experimental data were obtained from a compaction simulator (STYLCAM 200R). Elastic deformation of the press was determined through experimental tests on a calibration disk and integrated into the simulation. Numerical optimization was employed to characterize creep parameters. The inclusion of creep behavior in the simulations notably improved the agreement between numerical and experimental compression curves (stresses, thickness), particularly during the unloading phase of the compaction cycle. Significantly, this approach enabled the numerical reproduction of the observation that the minimum tablet thickness is not attained at the maximum compression stress. The findings underscore the necessity of considering creep behavior when employing FEM methods to model the compaction of pharmaceutical products.
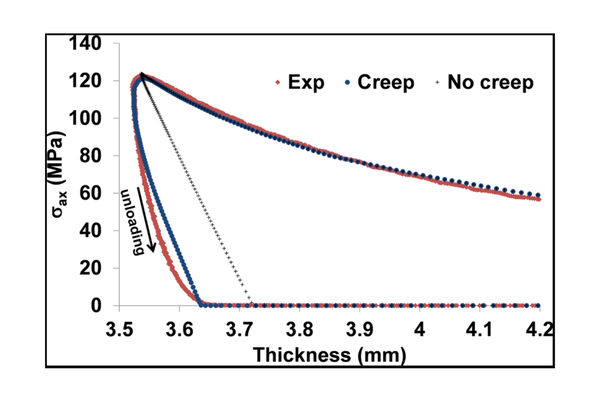
Comments
No comments posted yet.
Add a comment