Scientific papers
Roller compaction serves as a dry granulation process transforming powder blends into freely flowing agglomerates. When expanding or transferring the roller compaction process, maintaining comparable ribbon densities across scales becomes crucial for achieving similar tensile strengths and, consequently, akin particle size distribution in milled material. Consistent ribbon densities can be attained by upholding analogous normal stress applied by the rolls on the ribbon for a specific roll gap. Johanson's model (1965) is traditionally employed for predicting normal stress, but its practical application is constrained due to the need for an accurate nip pressure estimate and the assumption of a fixed angle of wall friction.
To address these limitations, we devised a novel approach utilizing roll force equations based on a modified Johanson model, eliminating the necessity for an estimated pressure value at the nip angle. An instrumented roll on the WP120 roller compactor collected data on normal stress at three locations across the roll width (P1, P2, P3), gap, and nip angle on the ribbon for both placebo and various active blends, along with corresponding process parameters. Nip angles were directly estimated using experimental pressure profile data from each run.
The roll force equation derived from the Johanson model was validated using normal stress, gap, and nip angle data from placebo runs. Calculated roll force values aligned well with those determined from the roll force equation provided for the Alexanderwerk® WP120 roller compactor. Subsequently, the calculation was reversed to estimate normal stress and corresponding ribbon densities as a function of gap and RFU (roll force per unit roll width). A placebo model was developed and calibrated using a subset of placebo run data from WP120, predicting ribbon densities with reasonable accuracy for active blends under varying process parameters.
The placebo model was then employed to calculate scale-up parameters from WP120 to WP200 roller compactor. While WP120 has a single screw speed, WP200 is equipped with a twin feed screw system. A limited number of roller compaction runs on WP200 were used as a calibration set to determine the normal stress profile across the ribbon width. The nip angle equation derived from instrumented roll data collected on WP120 was applied to estimate nip angles on WP200 under different processing conditions. The model successfully predicted ribbon densities for batches prepared on WP200, demonstrating the effectiveness of the scale-up procedure.
For demonstration purposes, the model was also calibrated using instrumented roll data from active C batches, showcasing its applicability when a sufficient quantity of API is available or the placebo model cannot predict ribbon density for active batches.
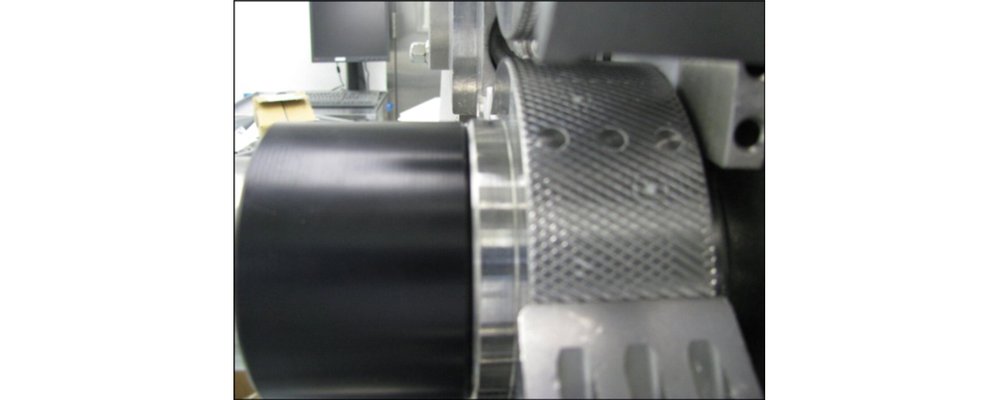
Comments
No comments posted yet.
Add a comment