Scientific papers
Compaction simulators are widely employed in tablet formulation and process development due to their flexibility, low material consumption, and advanced instrumentation, offering a comprehensive understanding of the compaction process. However, their ability to replicate essential aspects of rotary press compaction and their accuracy in simulating sub-processes such as feeding and filling necessitate systematic examination. This study assesses the impact of material deformation behavior, blend composition, and feeding on tensile strength and simulation accuracy compared to rotary presses of various scales. Overall, the compaction simulator exhibited commendable performance. The study revealed compaction profile sensitivity for highly visco-plastic materials and shear sensitivity in feeding for lubricated blends containing ductile particles. To address these issues, strategies for compensation are proposed, involving a meticulous analysis of compaction stress profiles over time and the introduction of a compaction simulator-adapted shear number approach. These approaches aim to reconcile differences in layout and operation mode between compaction simulators and rotary presses, facilitating a more straightforward determination of scaling process parameters and ensuring a faster and more reliable process transfer.
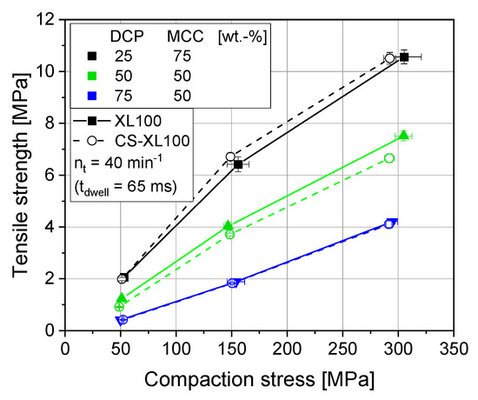
Comments
No comments posted yet.
Add a comment