Scientific papers
This study explores the feasibility of employing a compaction simulator and an oscillating mill as a material-saving approach to simulate a roller compactor for process development. Microcrystalline cellulose and dicalcium phosphate dihydrate were chosen to represent soft and hard materials, respectively. The relative density of ribbons and riblets was determined using a pycnometer, and the granule size distribution was assessed using laser diffraction. Tablet tensile strength and relative density were determined with a hardness tester and pycnometer, respectively.
The study demonstrated that the relative density of riblets and ribbons remained similar within the range of 1 to 12 kN/cm, indicating that the compaction simulator effectively mimics the compaction process of the roller compactor with a Kp of 1. The size distribution of granules produced by the oscillating mill and roller compactor showed similarity, indicating that the oscillating mill adequately replicates the roller compactor when using a comparable gap and sieve design. Ultimately, tablet tensile strength and relative density were found to be similar regardless of the granulation method applied and the material's deformation behavior.
In conclusion, the combined use of a compaction simulator and an oscillating mill effectively simulates the roller compactor, offering potential savings in material and time during the process development phase.
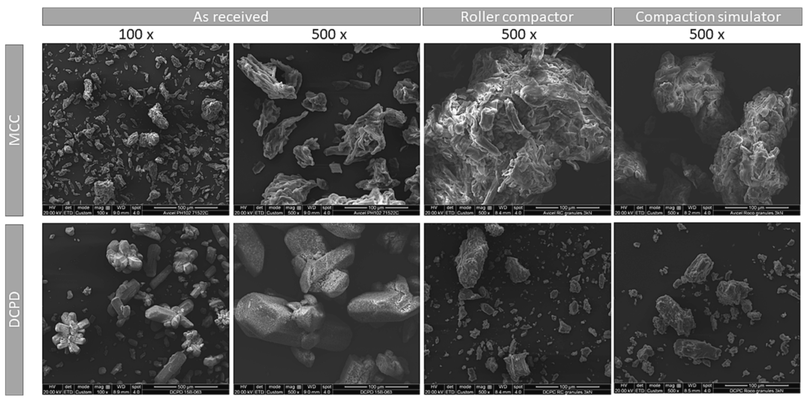
Comments
No comments posted yet.
Add a comment