Hot-melt extrusion: from theory to application in pharmaceutical formulation – where are we now?
Hot-melt extrusion (HME) stands as a widely acknowledged and robust technology, effectively enhancing the bioavailability of poorly soluble active pharmaceutical ingredients while offering an efficient continuous manufacturing process. The twin-screw extruder (TSE) serves as an incredibly versatile mixer, customizable to various needs, utilized for continuous compounding and granulation through different combinations of conveying elements, kneading elements (in forward and reverse configurations), and distributive mixing elements. TSE proves its efficiency across dry, wet, or melt granulation, facilitating the production of various dosage forms such as tablets, capsules, or granule-filled sachets, along with enabling the creation of innovative formulations like dry powder inhalers, granule drying units, nanoextrusion, 3D printing, complexation, and amorphous solid dispersions. Collaborations between academia and the pharmaceutical industry over recent decades have spurred novel advancements in HME technology, resulting in a notable surge in published articles and patents. This article synthesizes the challenges and methodologies involved in scaling up HME processes, while also delving into the advantages of continuous manufacturing, considerations of process analytical technology (PAT), and regulatory mandates. Ultimately, this comprehensive review expands upon previous works, delving deeper into the myriad possibilities afforded by twin-screw extruders (TSE) across various emerging applications.
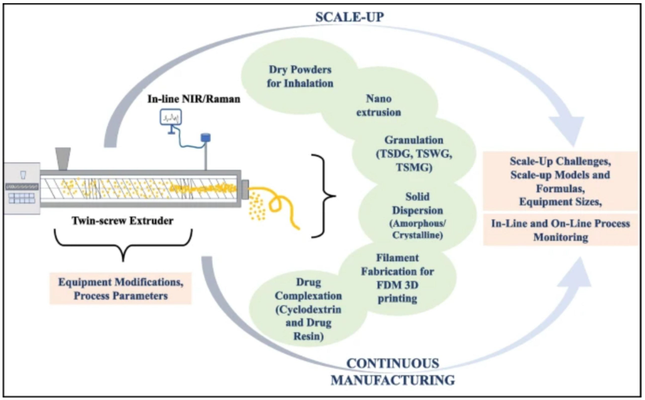
Comments
No comments posted yet.