Scientific papers
This thesis aimed to systematically investigate various types of roll compactors available on the market, characterized by differences in configuration, design, performance, and the flexibility to set process parameters. Ribbons were produced using inclined, horizontal, and vertical roll compaction designs, respectively. A comprehensive exploration of the impact of process parameters, roll compaction design, and material type on ribbon and granule characteristics was conducted through a design of experiments.
The performance of roll compactors was assessed based on the precision and deviation from the set value of HP/SCF and GW, depending on the roll compaction design and model materials used. The Mini-Pactor exhibited the best results for deviation, precision, and settling time of process data, while the BRC 25 roll compactor showed slightly higher deviations and less precise control in the test setting.
The investigation into the influence of material properties, process parameters, and roll compaction design on roll compaction focused on evaluating ribbon RD. The most significant process parameter was identified as HP/SCF, irrespective of the roll compaction design, type of roll compactor, or model material. Mannitol powder, with its sphere morphology and collapse under compaction, resulted in the densest ribbons. However, the fraction of MCC adversely affected ribbon RD due to elastic recovery after ejection from the nip zone.
Comparison between two ribbon RD measurement techniques, GeoPyc powder pycnometry (conventional) and x-ray µCT (more complex), favored GeoPyc for being easier, faster, and more cost-effective, while still providing accurate RD results.
Theoretical principles of process transfer were demonstrated, successfully achieving ribbon RD-based roll compaction transfer using calculated cf-s.
One of the challenges of roll compaction/dry granulation is the production of a high amount of fines, resulting in bimodal GSD. The amount of fines was shown to be influenced by set HP/SCF, GW, material type, and the type of roll surface for the AlexanderWerk BT120 and BRC 25 roll compactors. Ribbon RD and material type were identified as key factors governing GSD through the effects of roll compaction design and process parameters.
While roll compaction design did influence ribbon and granule properties, the study found that the impact of process parameters and material types was more significant, often overriding the effects of design.
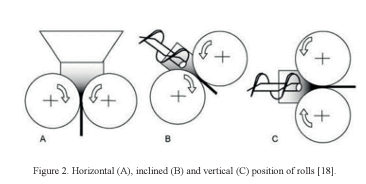
Comments
No comments posted yet.
Add a comment