Scientific papers
Twin screw granulation (TSG) has garnered substantial interest as a continuous wet granulation method in the pharmaceutical industry, with a primary focus on its study. Nevertheless, despite observations in various dry and batch wet granulation studies indicating that the granulation process influences final tablet strength, there remains a gap in understanding how continuous granulation impacts material compaction behavior. Consequently, exploring the material compactability and tabletability following continuous wet granulation is crucial for a comprehensive understanding of the twin screw granulation process and its effects on material behavior during tableting.
The primary objective of this study was to examine the influence of continuous twin screw granulation on the compactability and tabletability of commonly used excipients. Additionally, the study investigated the impact of binders on the compaction behavior of materials. Furthermore, the suitability of two "loss in compressibility" models—the Unified Compaction Curve (UCC) model and a porosity model—to predict the loss in tablet strength after twin screw granulation was assessed. Notably, these models had previously been applied exclusively to dry and batch wet granulations.
A full factorial design involving three variables (binder type, binder addition method, and the number of kneading elements) with two levels was employed for ConsiGma1 twin screw granulation. Formulations included microcrystalline cellulose (MCC), mannitol, or anhydrous dicalcium phosphate (DCPA) as the main excipient and polyvinylpyrrolidone (PVP) or hydroxypropyl cellulose (HPC) as binders. Magnesium stearate was added as a lubricant post-granulation before tableting. The study comprised 27 experiments, including a full factorial design and additional repetitions of granulation with PVP, dry binder addition, and four kneading elements for each main excipient. All granules were dried, milled, and subsequently tableted. Moreover, all formulations underwent direct compression to detect changes in compactability and tabletability after granulation.
The study assessed granulation torque, bulk density, and particle size distribution of the granules, as well as tensile strength and porosity of the tablets. Tabletability and compactability were determined based on compaction pressure, tensile strength, and porosity values. Parameters (PWG, TWG, and εWG) describing the loss in compressibility models were calculated.
MCC exhibited a loss in compactability and tabletability after twin screw granulation due to the hornification effect. In contrast, the compaction behavior of mannitol improved due to the formation of porous granules. The compactability of DCPA decreased, while tabletability increased moderately, likely owing to the brittle nature of DCPA. Additionally, binder type significantly influenced the compaction behavior, with PVP producing stronger tablets compared to the less hydrophilic HPC. However, the binder addition method played a minor role in modifying compaction behavior.
The UCC model proved applicable to MCC, detecting a loss in tabletability. Therefore, the model can be employed to predict tablet tensile strength when MCC is granulated with a twin screw granulator. Moreover, the UCC model can aid in designing the granulation process to achieve a target tensile strength based on small-scale preliminary studies, thus reducing the resources required for case studies. However, the UCC model was not suitable for mannitol and DCPA, as they experienced an improvement in tabletability after twin screw granulation. The porosity model was applicable to MCC and DCPA but not to mannitol, as it showed an improvement in compactability. The porosity model moderately described the loss in compactability of MCC due to a lack of tensile strength data points and the linearity of the tensile strength-porosity relationship. However, the model effectively described the loss in compactability of DCPA at tablet porosities achieved with compaction pressures used in the industry.
In conclusion, the results highlight that twin screw granulation can significantly impact final tablet strength, and the compaction behavior of the formulation may change depending on the materials used. Furthermore, the minor influence of the binder addition method on tablet strength suggests that the time-consuming binder dissolving process step can be omitted from the tablet production chain, enabling continuous manufacturing with twin screw granulation.
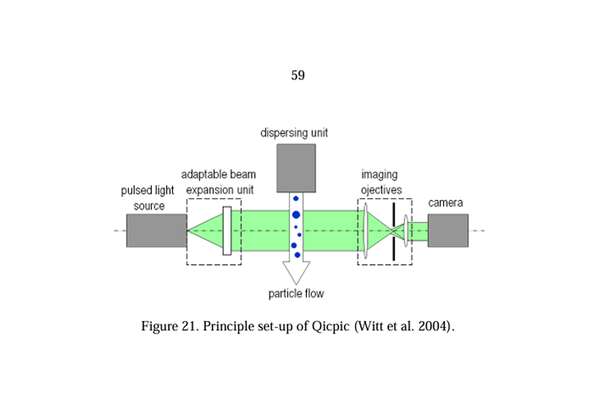
Comments
No comments posted yet.
Add a comment