Scientific papers
It is commonly accepted that compaction simulators can mimic the uniaxial compression process of roller compactors. To align the simulation output with actual product relative density, a correction factor (Kp) is often applied to the mathematical model, helping to account for machine-specific and scale-up variables. However, Kp is typically defined for a single material and within a limited process design space.
This study explores how material and process parameters—specifically roll speed, roll gap, and specific compaction force (SCF)—influence Kp during roller compaction simulation. Microcrystalline cellulose (MCC), starch, and a 50:50 % blend of both were selected as model materials. Relative densities of ribbons and riblets were determined using pycnometry, and Kp was calculated as the ratio of the respective relative densities.
Results showed that roll speed had a statistically significant effect on Kp for starch (p < 0.05), but not for MCC or the MCC:Starch 50:50 % blend (p > 0.05). Roll gap significantly influenced Kp across all three materials (p < 0.05). SCF also had a statistically significant impact on Kp for starch (p < 0.05), though its effect was not significant for MCC and the blend (p > 0.05). Additionally, a statistically significant second-order interaction (p < 0.05) was observed between roll gap and material type.
These findings highlight that Kp is sensitive to a combination of material properties and process conditions, underscoring the need for a formulation-specific approach when determining Kp in roller compaction simulations.
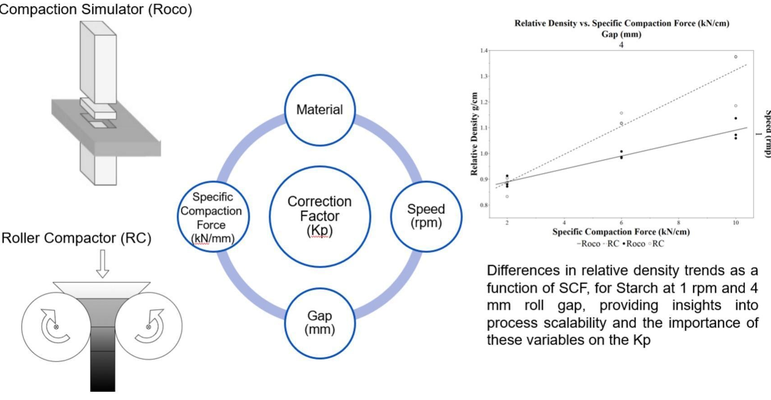
Comments
No comments posted yet.
Add a comment