Scientific papers
The Alexanderwerk® WP120 roller compactor incorporates instrumented roll technology, which was successfully developed and applied for measuring normal stress on the ribbon throughout the compaction process. The study investigated the impact of process parameters, including roll speed (4–12 rpm), feed screw speed (19–53 rpm), and hydraulic roll pressure (40–70 bar), on normal stress and ribbon density. Placebo and active pre-blends were utilized, where the placebo blend comprised a 1:1 ratio of microcrystalline cellulose PH102 and anhydrous lactose with sodium croscarmellose, colloidal silicon dioxide, and magnesium stearate. Active pre-blends were formulated with varying combinations of one active ingredient (3–17%, w/w) and lubricant (0.1–0.9%, w/w), while the remaining excipients remained consistent with the placebo.
Three force transducers (load cells) were strategically placed linearly across the roll's width, equidistant from each other, with one transducer positioned in the center. Recorded normal stress values from side sensors were lower than those from the middle sensor, displaying greater variability. Normal stress exhibited a direct proportionality to hydraulic pressure and an inverse relation to the screw-to-roll speed ratio. In active pre-blends, normal stress was also influenced by compressibility. For placebo pre-blends, ribbon density increased with rising normal stress, whereas for active pre-blends, ribbon density additionally depended on the gap.
Models established with placebo data accurately predicted ribbon densities for active blends, with improved accuracy as the drug concentration in the active blend decreased. The effective angle of internal friction and compressibility properties of the active pre-blend proved to be key indicators for predicting ribbon densities using the placebo ribbon density model. The feasibility of online ribbon density prediction during roller compaction was demonstrated through porosity–pressure data of the pre-blend and normal stress measurements. The study also explored the effect of vacuum de-aeration on placebo pre-blend, revealing that different vacuum levels did not affect normal stress values. However, complete cessation of vacuum led to an increase in normal stress, subsequently decreasing the gap.
The use of instrumented rolls showcased its potential to enhance fundamental understanding, thereby reducing the number of Design of Experiments (DOE) runs by elucidating the relationship between normal stress on the ribbon and process parameters.
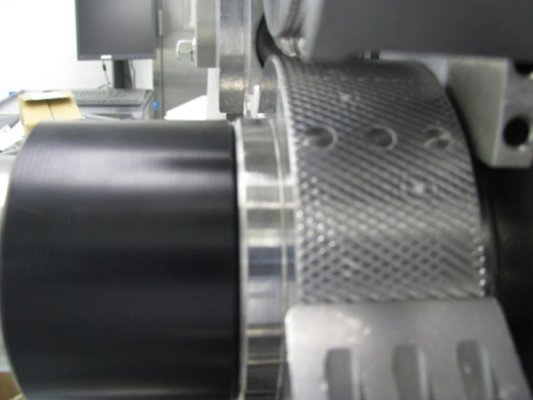
Comments
No comments posted yet.
Add a comment