Scientific papers
In the realm of pharmaceutical manufacturing, the primary goal is the consistent production of high-quality products. Simulation approaches offer the opportunity for virtual experimentation during the planning phase and the integration of digital twins in operational processes. The industrial processing of active pharmaceutical ingredients (APIs) into tablets involves a combination of discrete and continuous sub-processes with intricate interdependencies related to material structures and characteristics. The API and excipients undergo mixing, granulation if needed, and subsequent tableting. The structure and properties of the intermediate and final product are influenced by raw materials, parameterized processes, and environmental conditions, all of which are subject to certain fluctuations.
This study introduces, for the first time, an agent-based simulation model capable of predicting, tracking, and tracing the resulting structures and properties of intermediates in an industrial tableting process. The methodology for identifying and developing product and process agents in an agent-based simulation is detailed. Implemented physical models describe the impact of process parameters on material structures. To provide calibration and validation data, tablet production with a pilot-scale rotary press is experimentally characterized. Ultimately, the simulation results, predicting the final structures, are compared to the experimental data.
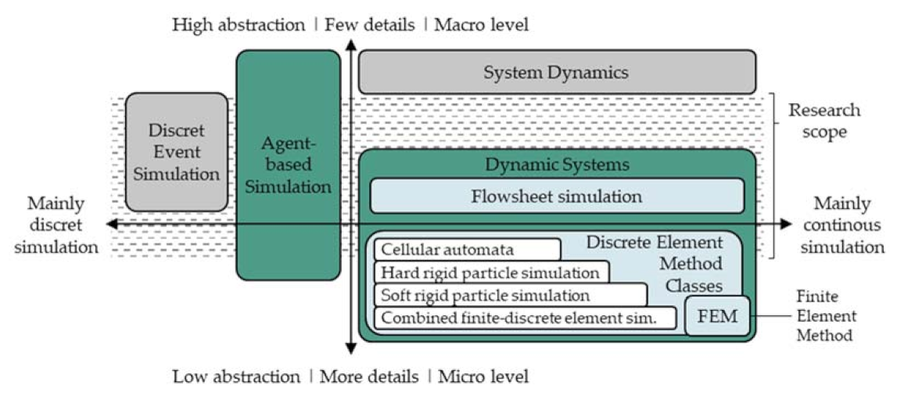
Comments
No comments posted yet.
Add a comment