Scientific papers
For decades, pharmaceutical industries have relied on batch processes for manufacturing medicine. However, these current practices are deemed inefficient, lacking sustainability and long-term competitiveness. Continuous manufacturing is emerging as a technology under scrutiny to address these challenges and achieve cleaner, more flexible, and efficient production processes. In continuous manufacturing, materials are continuously introduced, and products are continuously discharged, following a "one in, one out" principle. Various levels of continuous manufacturing integration can be identified, including partial integration of multiple connected unit operations, chain integration for chemical or pharmaceutical manufacturing lines, or full integration of all unit operations into a single end-to-end continuous manufacturing line.
This thesis focuses on facilitating end-to-end continuous manufacturing for pharmaceuticals/drug products, specifically targeting a wet granulation process. This was achieved by eliminating the traditional final drug substance manufacturing step (drying) and introducing the drug substance suspended in the washing liquid into a twin-screw granulator. The washing liquid served directly as the granulation liquid. The drug substance suspension feed in twin-screw wet granulation acts as the interface between chemical and pharmaceutical manufacturing in a potential configuration of an end-to-end continuous manufacturing process. The study demonstrated that feeding the drug substance as a suspension is comparable to the traditional drug substance blend feed in twin-screw wet granulation. This approach not only connects drug substance and drug product manufacture but also enhances process efficiency by eliminating a manufacturing step (drying).
Due to the omission of previous drying steps and the utilization of the original solvent for granulation, more extensive drying is required after twin-screw wet granulation. However, the research demonstrated that twin-screw wet granulation and drying can be amalgamated into a single process step, enabling further simplification of pharmaceutical continuous manufacturing. The concept of 'in-barrel-drying' utilizes the segmented temperature control of barrel zones of the twin-screw granulator. One compartment of the equipment operates at relatively low temperatures for wet granulation and material heating, while another compartment operates at very high temperatures for instantaneous drying. The study verified that high-quality dried granules suitable for compression could indeed be obtained using this approach.
By combining the drug substance suspension feed and in-barrel-drying concepts, two drying steps (before and after wet granulation) can be eliminated in a possible configuration of a fully integrated end-to-end continuous process chain. This represents a significant simplification in continuous manufacturing by removing time-intensive and expensive drying steps. Thus, this thesis makes a substantial contribution to the development of sustainable and competitive end-to-end continuous manufacturing for wet granulation processes.
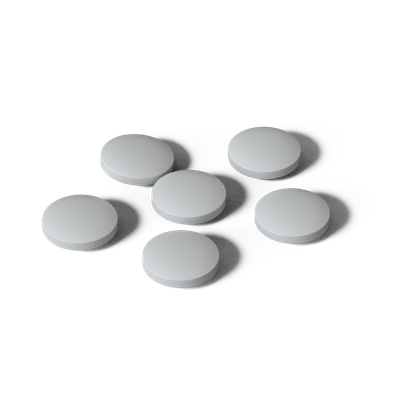
Comments
No comments posted yet.
Add a comment